Chemical Resistant Heavy Duty Epoxy Floorings
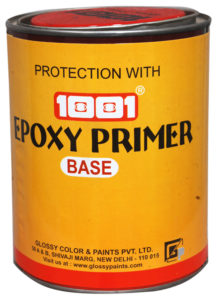
Literature of Chemical Resistant Heavy Duty Epoxy Flooring System
Description : |
Heavy duty flooring/linings are supplied in 3 pack system namely (A) Base (Unpigmented liquid). (B) Hardener-(unpigmented Liquid) . (C) Special Flooring Powder |
Thinning : |
Epoxy Thinner 0682T only |
Uses : |
Concrete Flooring |
Finish : |
Low sheen or as desired by the customer |
Application : |
By Trowel or Roller |
Covering Capacity : |
4-5 Sq. Metres Per Litre depending upon thickness (DFT) required and surface prepared and treated. |
Drying Time : |
Drying time · Touch dry : 2 hours. · Dry to handle : 8 hours · Hard dry : 24 Hours complete curing is for 7 days |
Color Range : |
As per Requirement from Glossy Enamel Shade Card ( for finish paints) |
Packing : |
4 litres, 20 litres. |
Highlights : |
|
Shelf Life : |
12 Months of base and hardener under sealed conditions |
Flash Point : |
Above 25°C |
Undercoats : |
Epoxy primer Grey/ off white/ red oxide |
Directions of Use : |
Chemical etching of floors and cleaning is of vital importance before painting commences. |
Application Areas : |
For Food & beverage factory floors, hospitals, pharmaceutical, electronics and fertiliser units, basement car parking areas. |
1001 EPOXY FLOORING PAINT 0640SG
LITERATURE/ TECHNICAL DETAILS FOR EPOXY FLOORING PAINT 0640SG
Epoxy heavy duty floor paints are especially manufactured with best quality inert pigments and extenders having excellent acid, alkali and chemical resistance properties in order to protect concrete surfaces. This specification is intended to cover technical aspect and the method of application. The composite system is as follows-
1. Antiset (Unpigmented Primer 2 pack) (Ratio 2: 1, by volume, Base to Hardener)
2. Epoxy Floor Putty 2 pack where the surface needs leveling and crack filling.
3. Finally Finish / Top Coat (pigmented) any shade 2 pack (Ratio 4:1, Base to Hardener)
SURFACE PREPARATION AND METHOD OF APPLICATION FOR EPOXY FLOOR PAINT SYSTEM
Step 1- Old Concrete surface must be freed from laitance, traces of grease, oil or moisture and ensure the complete removal of dust particles. Degreasing is preferably carried out with non – flammable chemicals and dust etc. by sand blasting. If sand blasting is not possible, follow the procedure as below.
Step 2- CHEMICAL ETCHING IS ONLY REQUIRED FOR FRESH CEMENTED SURFACES.
Chemical etching / pretreatment Reducer is applied by brush over the new floors liberally and left in contact for 15 minutes. This is then washed off with plenty of water followed by thorough drying with cloth.
Step 3- Finally clean the entire etched surface (Floors) with Cleaning Reducer/ Glossy Reducer 013T. Cleanliness, roughness and dryness of the surface is a prerequisite for good adhesion of Epoxy flooring system (Paints and Primer).
Step 4- FOR FILLING CRACKS / UPROOTED SURFACE OF THE FLOOR :
Make special putty at the site. The base resin of unpigmented Antiset Primer is to be mixed properly with 3 to 4 times of Chemical Compound (screed/ filler), and then add the hardener part to the mixture. Apply this immediately by trowel or chisel where filling is required. In simpler words, mix 2 parts base with 4 parts of screed then add 1 part hardener.As the pot life of this putty is very short at Room Temperature, try to apply immediately, otherwise it would gel. Pot life is hardly 30 minutes.
Step 5 - (a) Mixing Ratio for Antiset Primer 2k – Mix Base & Hardener in the Ratio of 2:1 by volume.
(b) Mixing Ratio for Floor Finishing Paint 2k – Mix Base & Hardener in the Ratio of 4:1 by volume.
Step 6- One coat of antiset primer (2 Pack) is applied on the pretreated surface by Brush / Spray or Trowel. The primed surface should be allowed to remain tacky prior to application of Epoxy High Build Finish/ Top Coat. The Covering of this primer is 3.5 to 4 sq mtr per litre per coat. D.F.T. is approximately 60 to 80 microns.
Step 7- Use finished paints only after 2 – 3 hours of primed surface. Ensure that the primed surface must be tacky, so that finished/top coat High Build Epoxy Paint would have proper bonding.
COVERING :- 10 – 12 sq mtr per litre per coat with 60 – 80 microns D.F.T. depending on the thickness of coating and manner of application.
NOTE: The primer must not be fully cured otherwise curing of epoxy paint system is very difficult below room Temperature 20°C. Complete curing of the system takes place at Room Temperature (25 – 30°C) in seven days but if room Temperature is below 20°C, curing period would be extended by another week. Movement of light traffic may resume only after 48 hours of curing. Iron wheel–cart is allowed only after 7 days of perfectly cured film i.e after mar- resistance is achieved.
PRECAUTION :- As the pot life of epoxy primer, epoxy putty and epoxy finish/ top coat is very short, limited quantity of base and hardener are only to be mixed which can be used within 30 minutes.